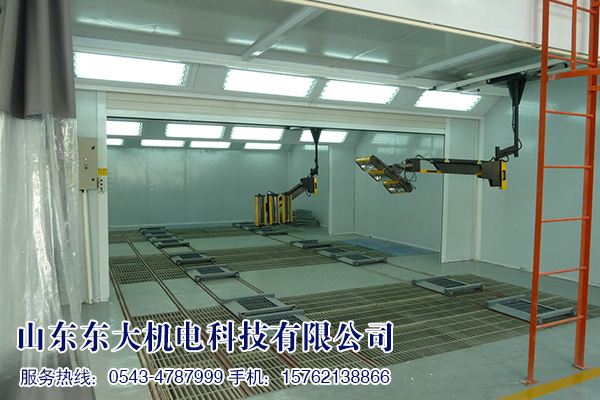 |
Sheet metal lacquer line 3
Hits:643
Time:2018-05-10 14:49:24
|
Description
Product overview:
The sheet spray flow operation is the extension of lean production from automobile manufacturing to automobile maintenance. It refers to the replanning of the sprayed workshop, the use of specific methods to transform the workshop into different functional areas, and the specific work personnel to complete the specific work method. Since the different processes of the vehicle to be repaired are completed in different areas and by different mechanic operations, it is similar in form to the &ldquo of the automobile factory; the pipeline ” therefore, it is called “ the flow operation ” According to its implementation form, it can be divided into hardware flow and process flow. According to the linking mode of each process, it can be divided into non beat flow and beat flow. The traditional mending paint process is the complete work of 1-2 people to complete the repair. One repair process contains more than 10 process contents, and the sheet jet waterline is the reasonable decomposition of the process of paint repair, and the division of labor for the equipment and personnel according to the process flow. So, a complicated thing is simplified, a complete repair process is generally divided into 7-9 workstations, (sheet metal, scraping, grinding, priming, cover, paint, drying, throwing, assembly). Each family is flexible in choosing the number of workstations for each workstation according to their own circumstances. The workstations are almost similar. Each workstation adjusts the work of each repair car according to the workload of each repair car. It is responsible for the work of different working procedures to ensure that the working hours of each station are similar. Like the assembly line of the car assembly, the working hours of the technicians of each workstation are strictly controlled to ensure that the vehicle is in accordance with the plan. The maintenance quality of each workstation is also strictly controlled to ensure the quality of maintenance after completion. All vehicles are completed according to the expected time.
The composition of the workspace:
Type of sheet metal spray line
Form of work position
DD-2 (2 Station)
Ground grinding station and spray drying station
DD-3 (3 station)
Fill up the work position and primer in the work place and primer.
DD-4 (4 station)
Fill up the work place, the primer paint, the top coat, the paint, and the finish.
DD-7 (7 station)
Soil grinding station, soil grinding and drying position, priming position in primer, drying and grinding position in middle coating, sheltered sticker position, topcoat painting position and topcoat drying site
DD-9 (9 station)
Multi function soil grinding station, soil grinding station, soil grinding and drying position, priming position in primer, drying and grinding position of middle coating, covering sticker, topcoat painting position, topcoat drying station, and assembly and polishing station
DD-11 (11 station)
The fast repair sheet metal position (2 sets), the soil filling position, the grinding position, the primer drying position, the finishing position after the primer, the drying position in the middle coat, the grinding position after the middle coating, the covering sticker, the paint painting station of the face paint, the drying site of the topcoat
Construction process
1, sheet metal correction: first, the technical staff of the sheet metal correction workstation will put the clean vehicles on the track line, after completing the correction and disassembly work, the vehicle moves along the track to the scraping dust (scraping putty) work position;
2, ash scraping (scraping putty): after the dust scraper checks the quality of the sheet metal correction, after the surface of the workpiece is treated, the dust can be scraped, the natural drying or the infrared baking is selected, and the vehicle is moved to the working position of the grinding operation after completion;
3, grinding operation, grinding personnel according to the process needs to choose appropriate sand paper and grinding tools, work, after the completion of the homework to move to the next finish;
4, primer: primer working technician inspecting the quality of soil and grinding, finish the painting of primer, two finish grinding and so on. After completion, the vehicle moves along the track to the sheltered position;
5, covering: the masking technician inspecting the quality of the primer for the non spraying surface, and cleaning all the cracks with compressed air, and moving the vehicle to the spray paint room after the curtain is completed;
6. Spray paint: after checking the masking quality, the painting technician clean, spray, and finish the vehicle moved to the paint room;
7, baking: the paint operators set the time and temperature according to the paint, start the machine and monitor the equipment work, the roast paint has sound and light alarm, the vehicle cooling after the release;
8, polishing:. After the polishing technician inspecting the quality of the spray paint, select the type of wax according to the size and size of the surface of the vehicle, the polishing, the cleaning operation, and the vehicle being sent to the assembly station after completion;
9, assembly: the assembly technician will complete the assembly of the disassembled parts. The repair work has fully completed the sheet spray water line to improve the capacity of the mending lacquer vehicle by 35%, the technician's overtime time reduced by 90%, the cycle of the repair paint of the car owner shortens 50%